Cooling Tower Corrosion Monitoring with Digital pH, ORP, and Conductivity Sensors
Cooling towers release heat from circulation water. The towers are critical and require proper maintenance to prevent unexpected and costly shutdowns. Scaling affects efficiency and performance. Corrosion shortens the useful life of the system. Lastly, bacterial colonies, such as legionellae, cause significant health risks. Plants use pH, ORP, and conductivity sensors on their cooling towers to prevent and control these issues.
pH Sensors Prevent Scaling and Corrosion
Cooling towers require an acid addition like sulfuric for pH adjustment to dissolve the calcium carbonate buildup from high salts in the system. Dissolving the calcium carbonate reduces scaling, which helps the system’s efficiency. Additionally, monitoring the pH adjustment with a digital Memosens® sensor such as the SE 554 provides improved corrosion control and earlier detection of process breakthrough achievable.
A responsive pH sensor like the Knick SE 554 features:
-
An open junction that resists plugging from biocides
-
Extended sensor life and fewer calibrations due to the reference system design and construction which resists poisoning
-
A hermetically sealed sensor head that is fully submersible
ORP Sensors Monitor Oxidizer Levels
As part of the cooling tower control system, a chemical skid usually doses an oxidizer to sanitize the water. The ORP sensor infers the concentration of the oxidizer, such as sodium hypochlorite. A reliable ORP measurement ensures oxidizer levels are adequate to prevent bacterial contamination. Consequently, this contamination can lead to potential health issues for plant personnel. The SE 564 provides accurate and repeatable ORP monitoring to help maintain a healthy cooling water system.
The SE 564 digital ORP sensor is well suited for cooling towers due to its:
-
Open junction which resists plugging from biocides
-
Platinum electrode that is insensitive to oxidizing chemicals found in the cooling tower
- Offline calibration capability that makes the sensor’s calibrations more accurate
Conductivity Sensors for Blow Down Control
The automatic blowdown control system in cooling towers requires a conductivity measurement of the water. This measurement controls when high conductivity water is “blown down” or removed, and “new” low conductivity makeup water enters the system. The SE 630 is a rugged conductivity sensor that will resist corrosion and provide a long-lasting and repeatable measurement.
The Knick SE 630 conductivity sensor utilizes:
-
A Kynar sensor body and graphite electrode construction are resilient in corrosive environments like cooling towers
-
Digital Memosens technology with sensor health diagnostics, allowing the user to prevent measurement failure
Sensors Made for Wet Environments Like Cooling Towers
A traditional analog sensor connection is typically not submersible, making it an issue for moist environments like cooling towers. Manufacturers will “pot” the cable into the sensor to get around this. However, this requires the customer to completely disconnect and pull the sensor cable from the transmitter during maintenance.
Digital Memosens sensors have inductive connections which are entirely submersible. Operators can connect the sensors in the wet environment without concern of failure. In addition, technicians can do all calibration and maintenance on the Memosens sensor in the shop or lab. Memosens sensor/cable connections are available for pH, ORP, and conductivity measurements. You can use the sensors in conjunction with a Stratos Multi transmitter. This transmitter has sealed moisture-protected circuit boards. Consequently, this design provides a long service life.
What will be the Return on Investment for your Cooling Towers?
- Reduction in Maintenance Time and Costs:
By using the SE 554, SE 564, SE 630, and Stratos transmitters, you can expect to perform fewer calibrations as well as less frequent sensor replacements. Therefore, you will use fewer sensors. Reduced frequency of calibration/replacements equals fewer trips to the towers and reduced cost over the sensor’s lifetime. - Automated Control of Cooling Tower Chemistry:
Automated control of cooling tower chemistry is possible with digital pH, ORP, and conductivity sensors. As a result, you will find a lower consumption of chemicals and water usage, which will extend the life of the cooling towers.
Products Featured in this Application
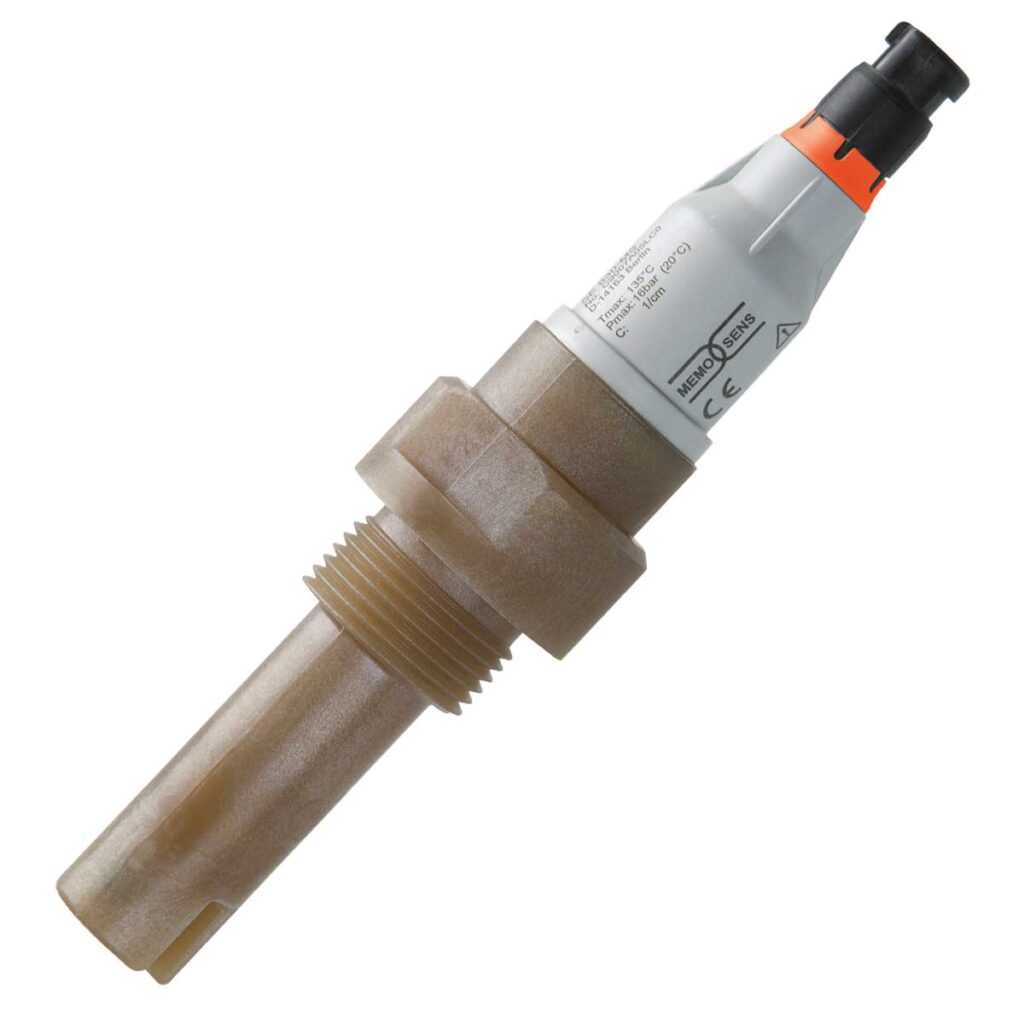
SE630
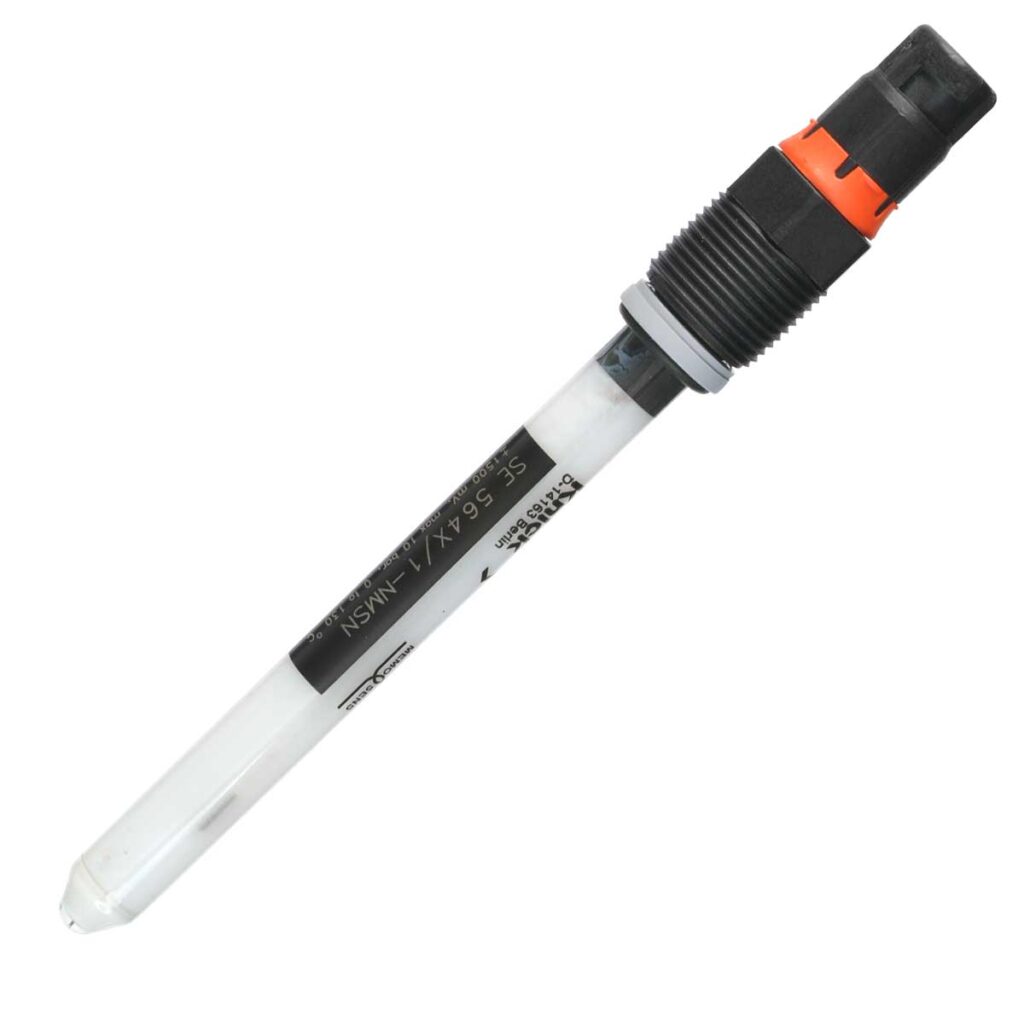
SE564
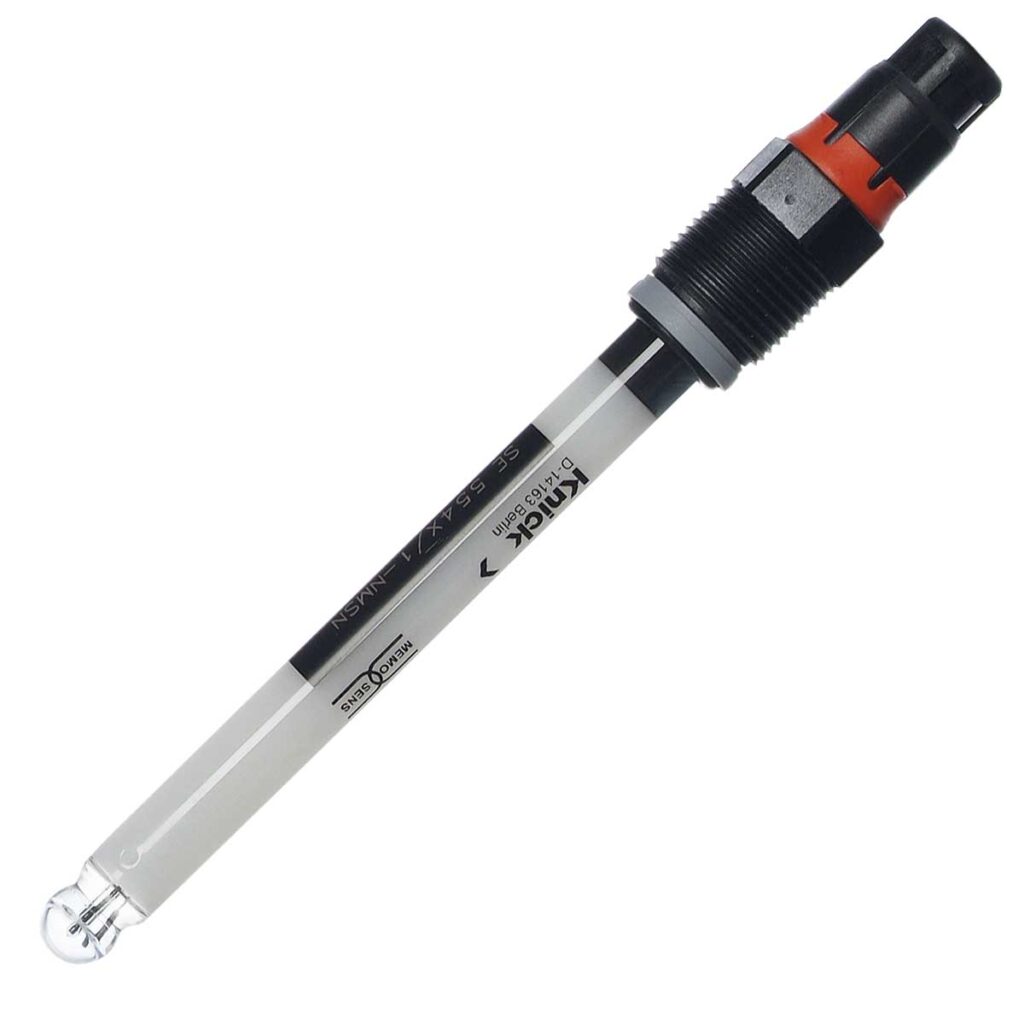